Reflections on My Visit to Tontarra Medizintechnik– By Dan Coole, Managing Director, Surgical Holdings
During my recent visit to Tontarra, a family-run business in Wurmlingen, South Germany, I was extremely impressed by their commitment to precision, quality and sustainability. Established in 1966, Tontarra is now in its third generation of leadership, with over 160 employees. They are renowned not only for manufacturing their own Tontarra-branded range but also for their contract manufacturing work with industry giants.
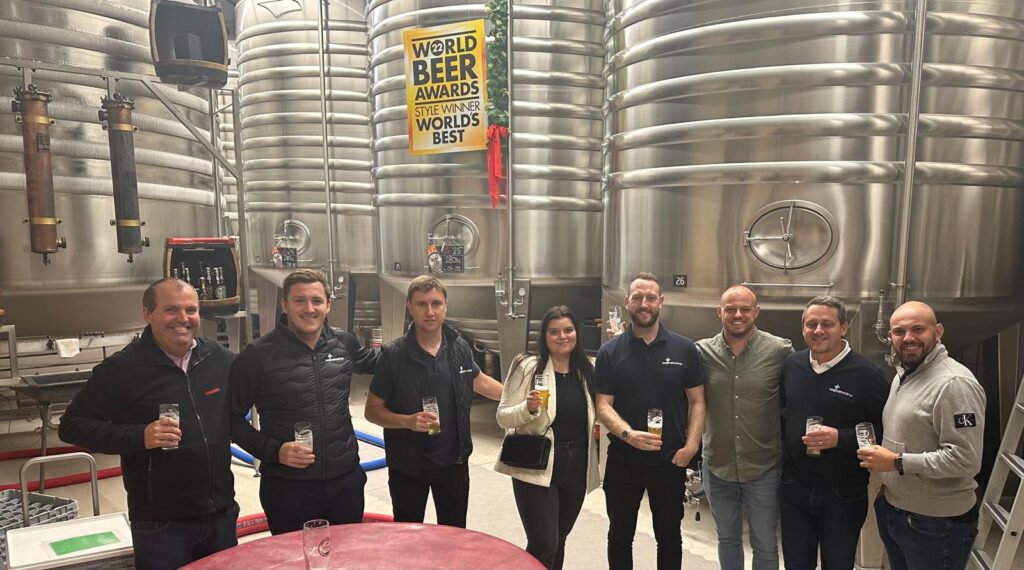
What stood out to me was the sheer scale of their production and its intricacy. For example, they produce over 50,000 Debakey forceps annually. The precision of these instruments is achieved through the use of cutting-edge automated CNC technology, including 5 & 7-axis CNC machines. These machines cut from solid material bars to size in-house, ensuring tight automated quality control at every stage of manufacturing. Robots are utilised for replenishing raw materials and tooling, which is extremely slick.
The production process at Tontarra involves some key stages including milling/turning, assembly, finishing and quality control with a purpose-built automated cleaning/passivation line. Their CNC machines ensure highly precise, consistent products, while the assembly is performed by skilled technicians who undergo a three-year apprenticeship. Their dedication to quality is evident in the final stages of the process, where each product is meticulously inspected by a 10-member quality team using microscopes. Any imperfections are photographed for traceability. The finish that’s possible from using CNC machines continues to improve, with some machined components presenting a near perfect polished surface.
I was particularly interested in their Kerrison Rongeur range, which includes both fixed and take-apart models. Their innovative Cleanwave design offers the stability of a fixed Kerrison while enhancing cleanability, reducing friction through carefully engineered cutouts. This is a great solution for addressing the growing concerns around SSD (Sterile Services Departments) and infection control. Their Kerrisons also feature options like ceramic coatings, gold springs for quick identification, and bone ejectors. Tontarra have also taken the crucial step of specifically validating the CleanWave for decontamination and sterilisation.
Their arthroscopy punch range, equivalent to industry standard brands, is competitively priced and manufactured with the same high precision using CNC technology. I was also impressed by their endoscope range, available in a variety of common sizes including laparoscopic, cystoscopic, hysteroscopic, and arthroscopic options, with HD, HD+, and 4K options, with availability from stock being a key benefit. This works well in synergy with our in-house scope repair service for beyond repair trade-ins, ensuring customers have access to the latest technology with minimal downtime.
One of the highlights of the visit was learning about Tontarra’s sustainability initiatives. They recycle waste materials ethically, capture and repurpose heat generated from their machines to control the temperature in the factory, and recently installed solar panels to generate renewable energy. Their cooperative efforts with local businesses further reflect their commitment to sustainability.
Visiting Tontarra reaffirmed my belief in the value of craftsmanship, innovation, and responsibility in medical device manufacturing. They balance precision engineering with sustainable practices, ensuring that every instrument produced meets the highest standards while minimising their environmental footprint. It was a valuable experience, and I look forward to continued collaboration with this impressive company.